Service is in our DNA
We offer individual and comprehensive service over the entire product portfolio.
Benefit from our years of experience and let our technical know-how support you continuously in all topics – from after sales to innovation planning.
One-stop Service Workshop
Our headquarter comprises of an in-house service workshop for the full-line repair of our core components. The scope of repairs is tailored to the individual needs of each customer and can include complete outsourcing concepts of frequent equipment repair requirements.
Another essential part of our workshop is the state of the art facility for the application of powder sprayed wear resistance coatings.
In addition to standard repairs, we offer our customers the opportunity to test new repair service capabilities for their feasibility in our workshop.
- Repair and coating of galvanizing line pot equipment
- Repair and coating of strip processing line furnace rolls
- Repair of core components out of the DUMA-BANDZINK product portfolio
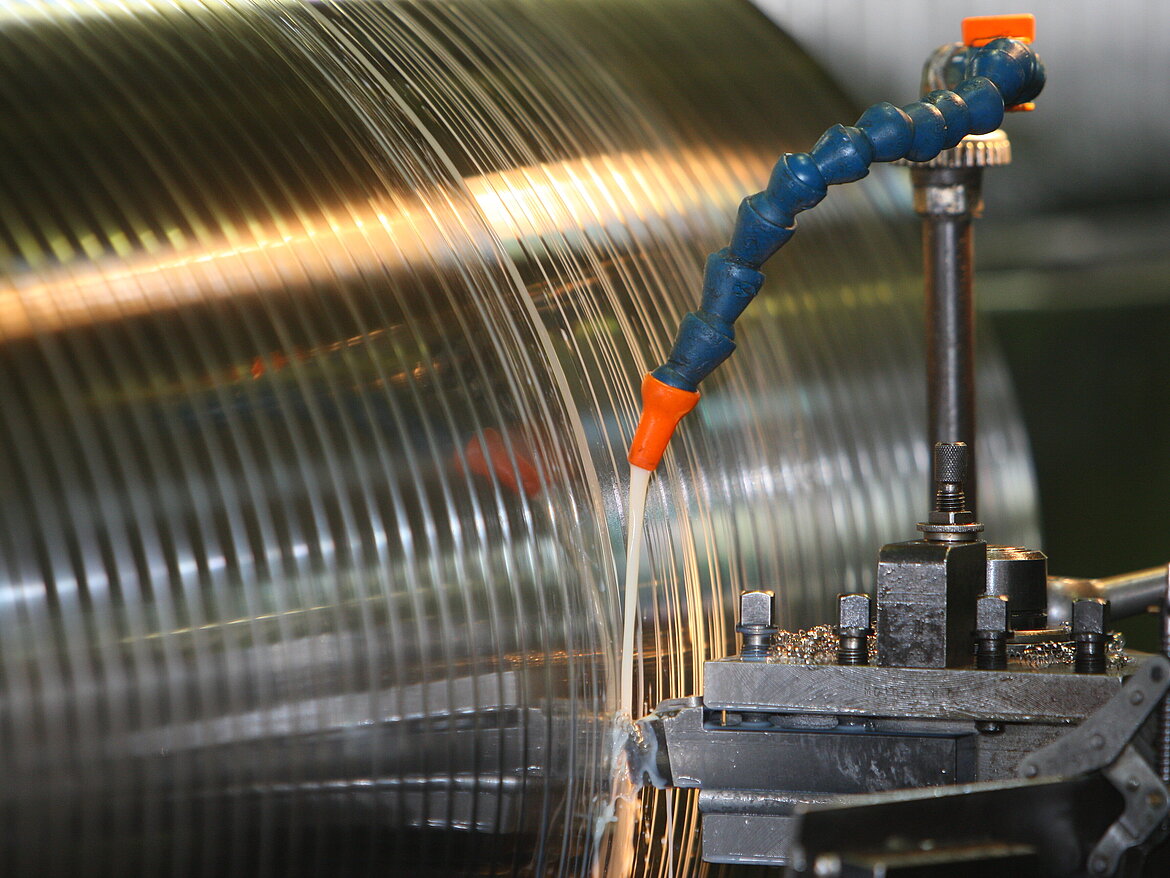
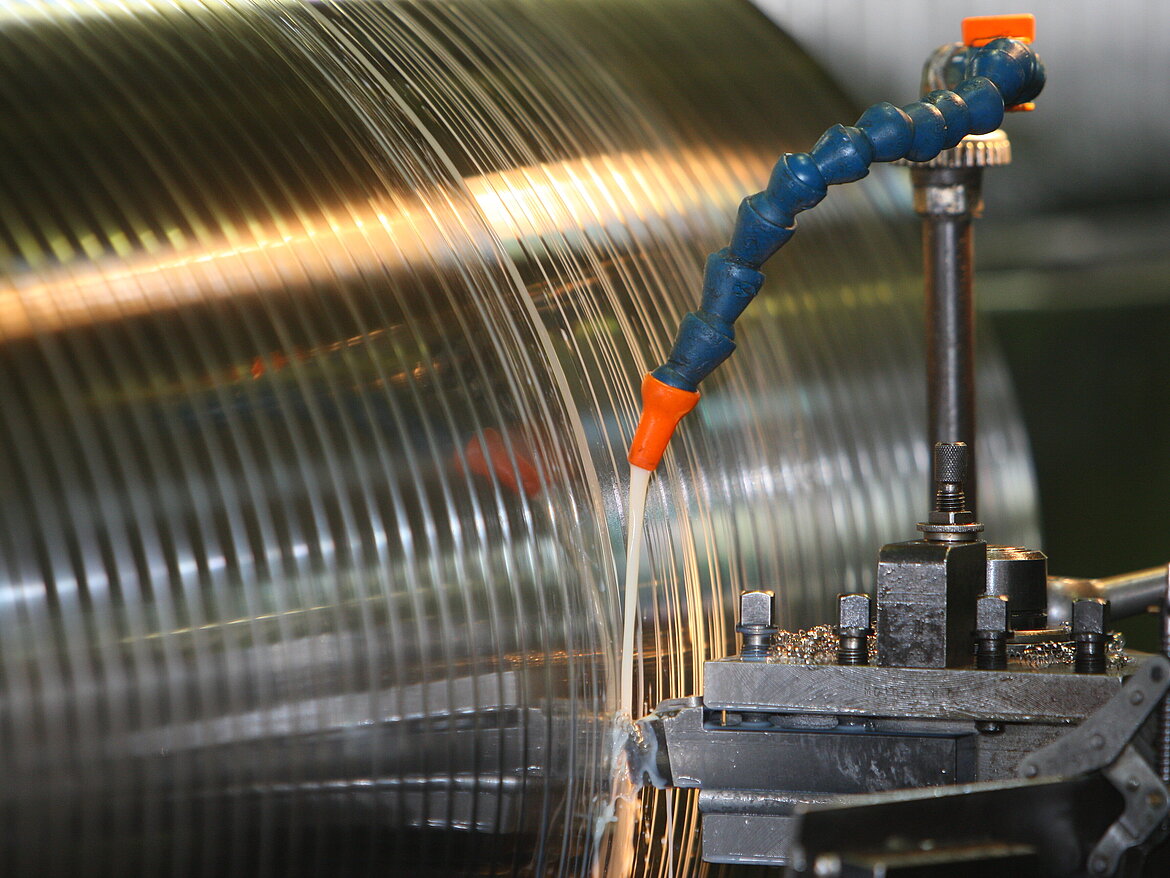
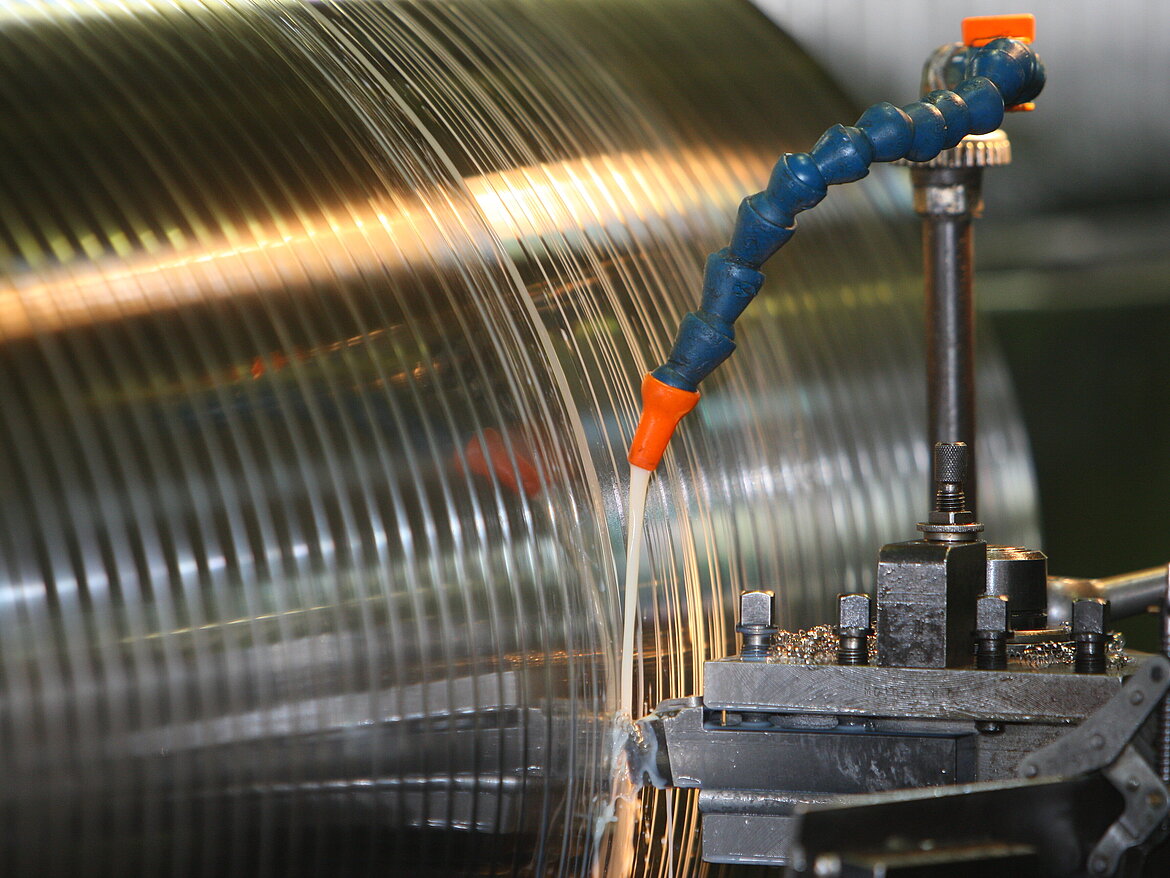
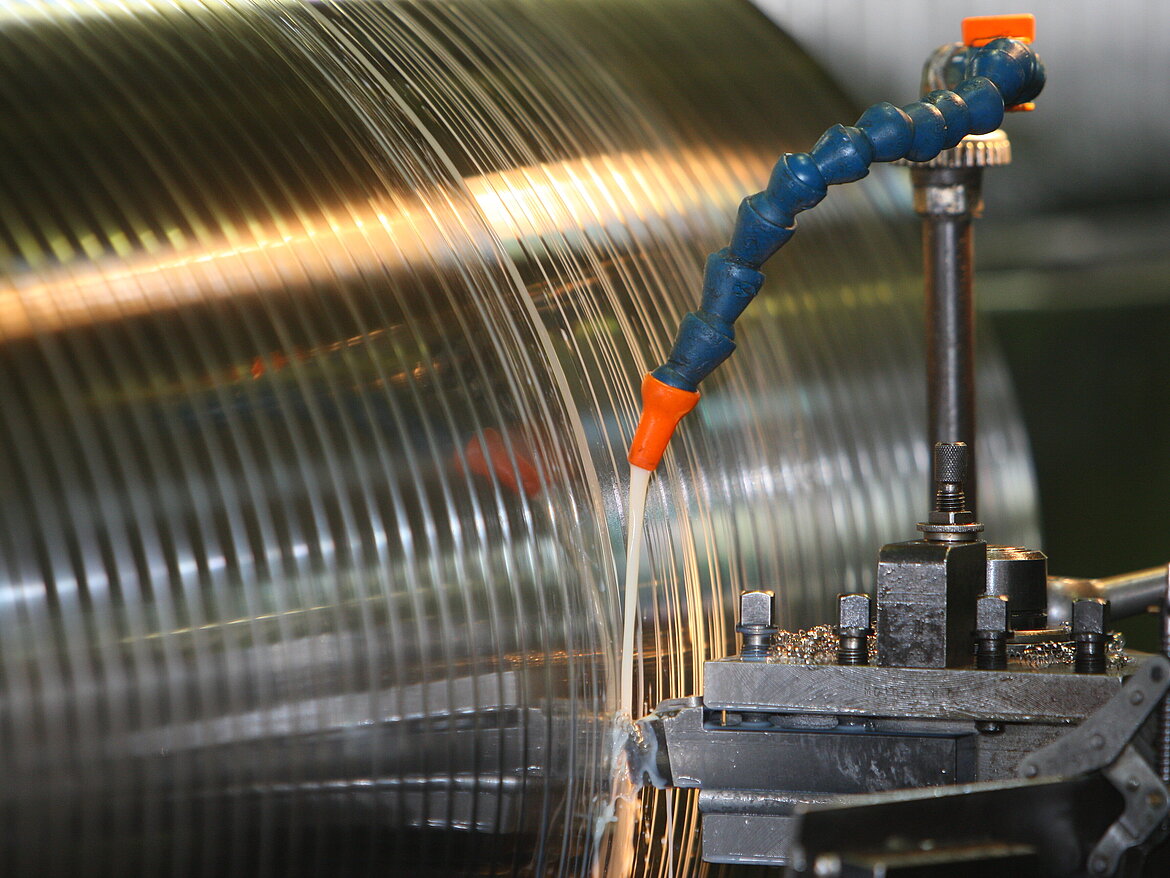
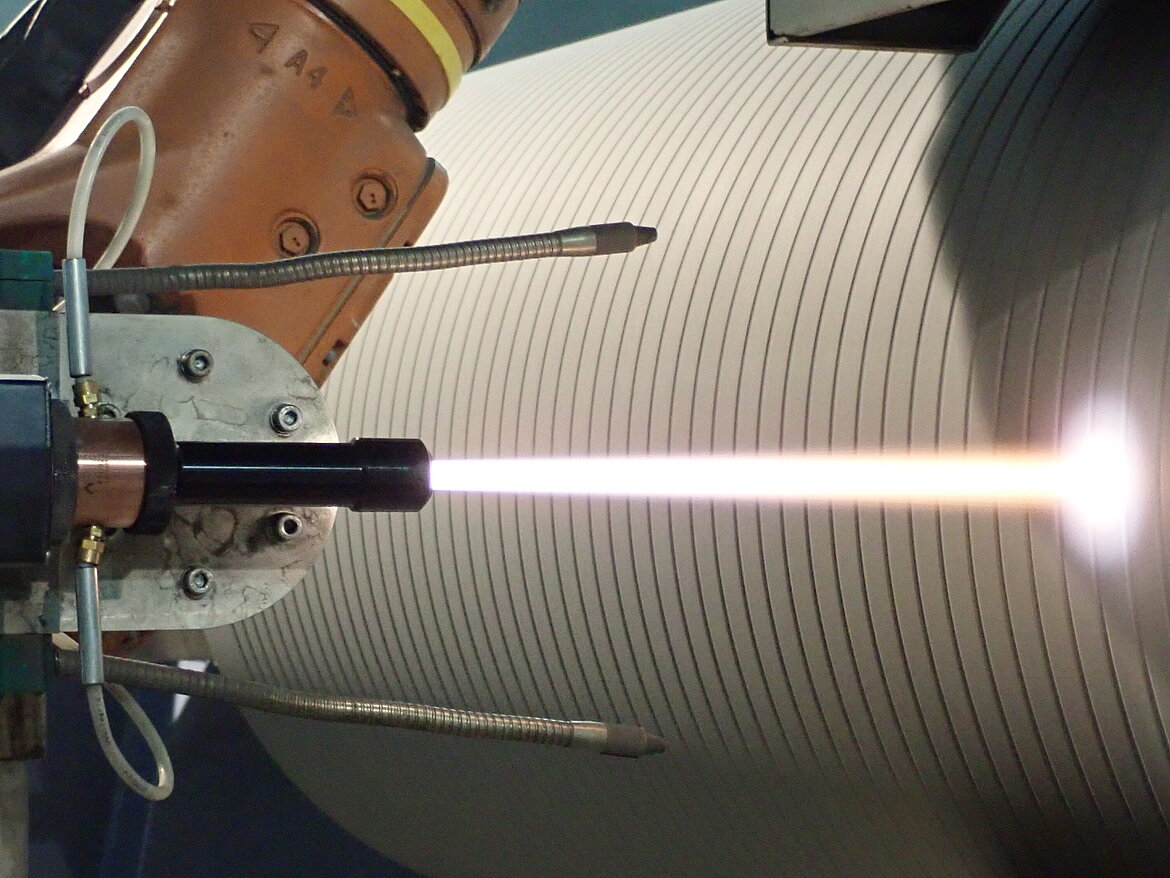
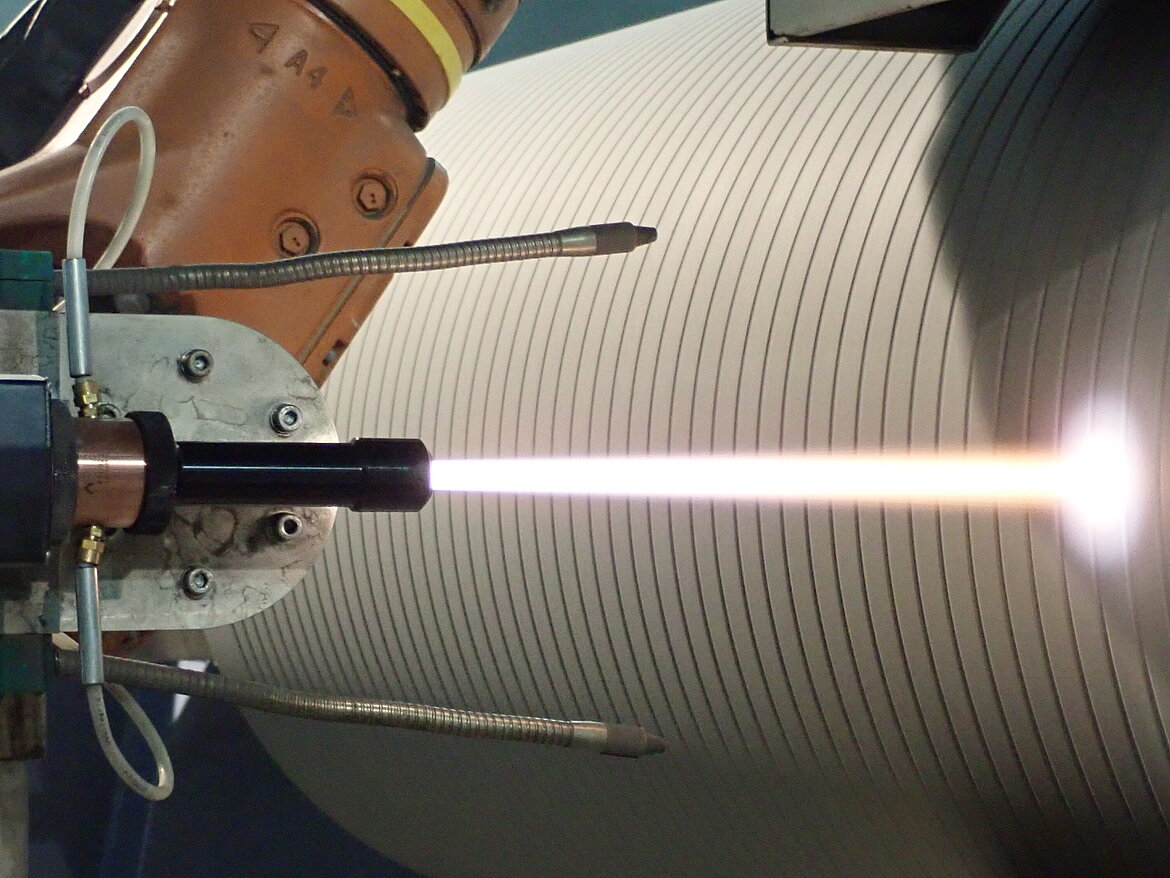
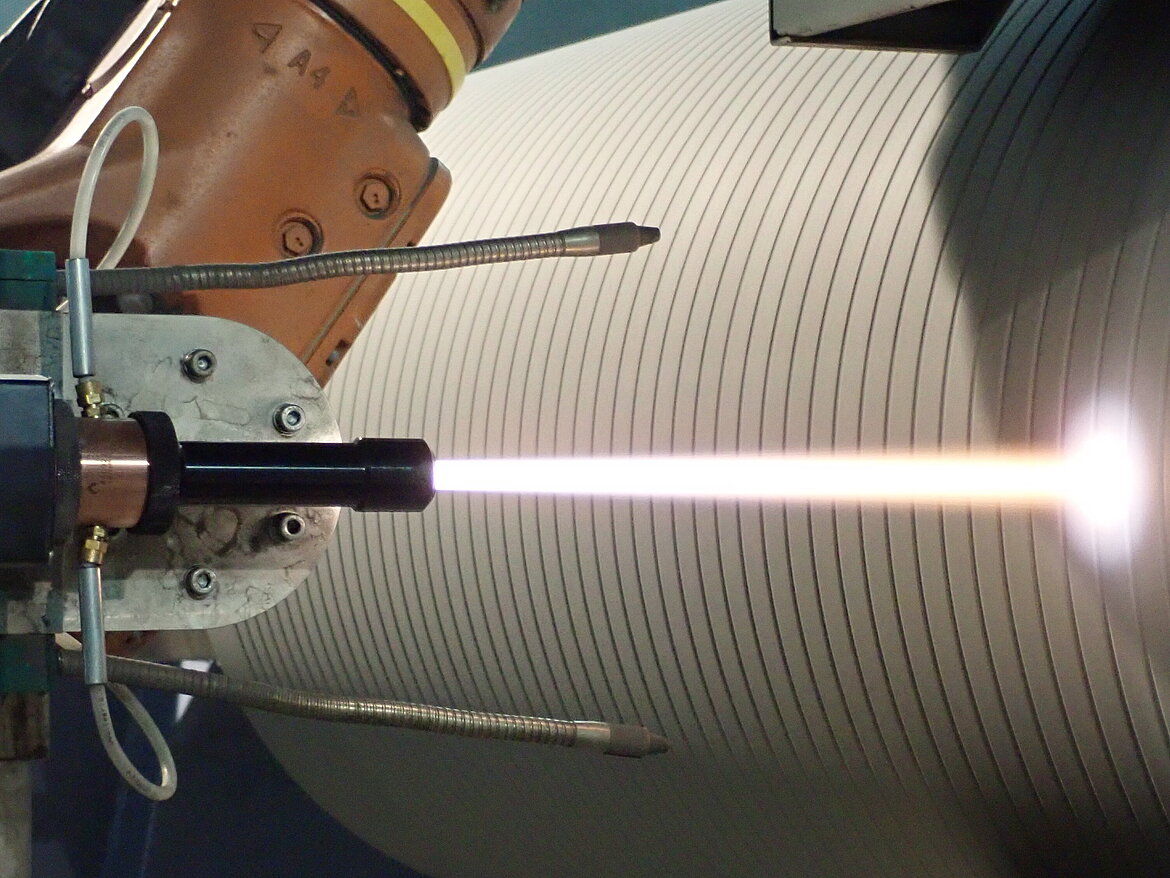
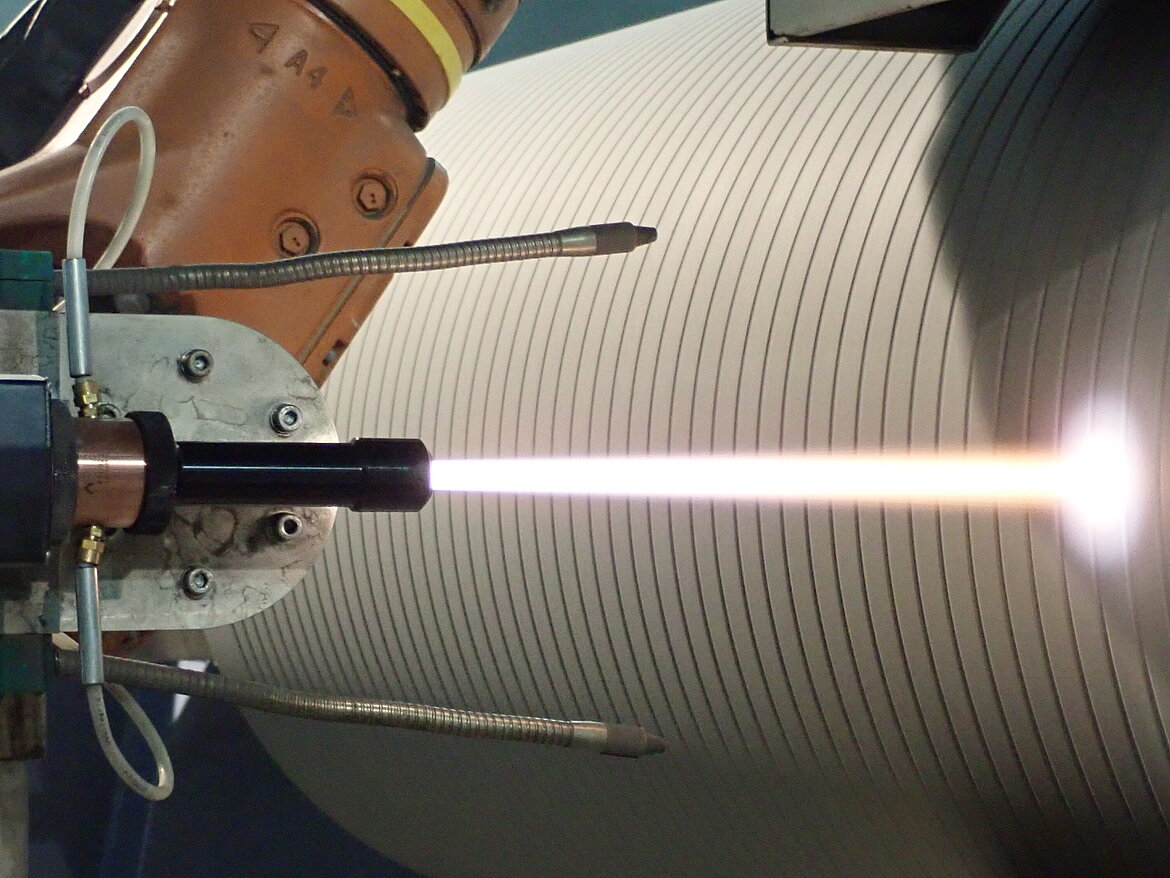
Key Account Support
DUMA-BANDZINK offers individual key account support for all customers. The key account manager continuously supports the customer in all important matters of operating, maintaining and optimizing the performance or DUMA-BANDZINK installations and equipment. It is our priority to take into account the individual and specific requirements of each customer.
- Product innovation with DUMA-BANDZINK as a technical development partner
- Continuing on-site support and joint continuous improvement committees
- Optimizing the performance of all core components and equipment out of our product scope
- Redesigning and modification of existing equipment to increase production efficiency
Trusted Partner
We offer a wide range of services at our customer´s premises. These include on-site equipment checks and inspections ranging from one-time assignments to ongoing maintenance and inspection frame agreements. Concerning spare parts supply concepts, we have consignment stock agreements in place with our high profile customers in order to ensure the highest level of availability with the least effort on recurrent internal processes.
- On demand and preventive equipment maintenance and inspections
- Maintenance and spare parts management concepts from a single source
- Frame agreements and partnership contracts offering long-term savings on OPEX and maintenance budget expenditures
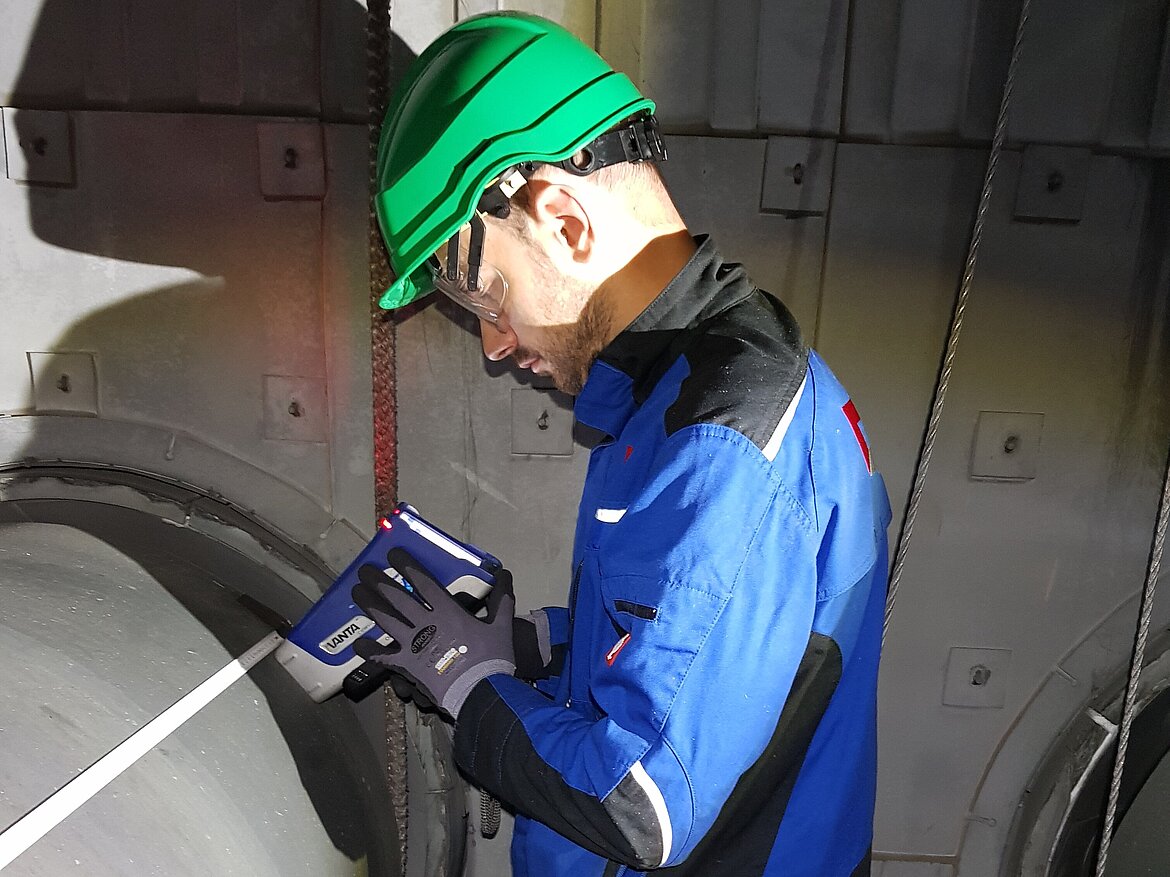
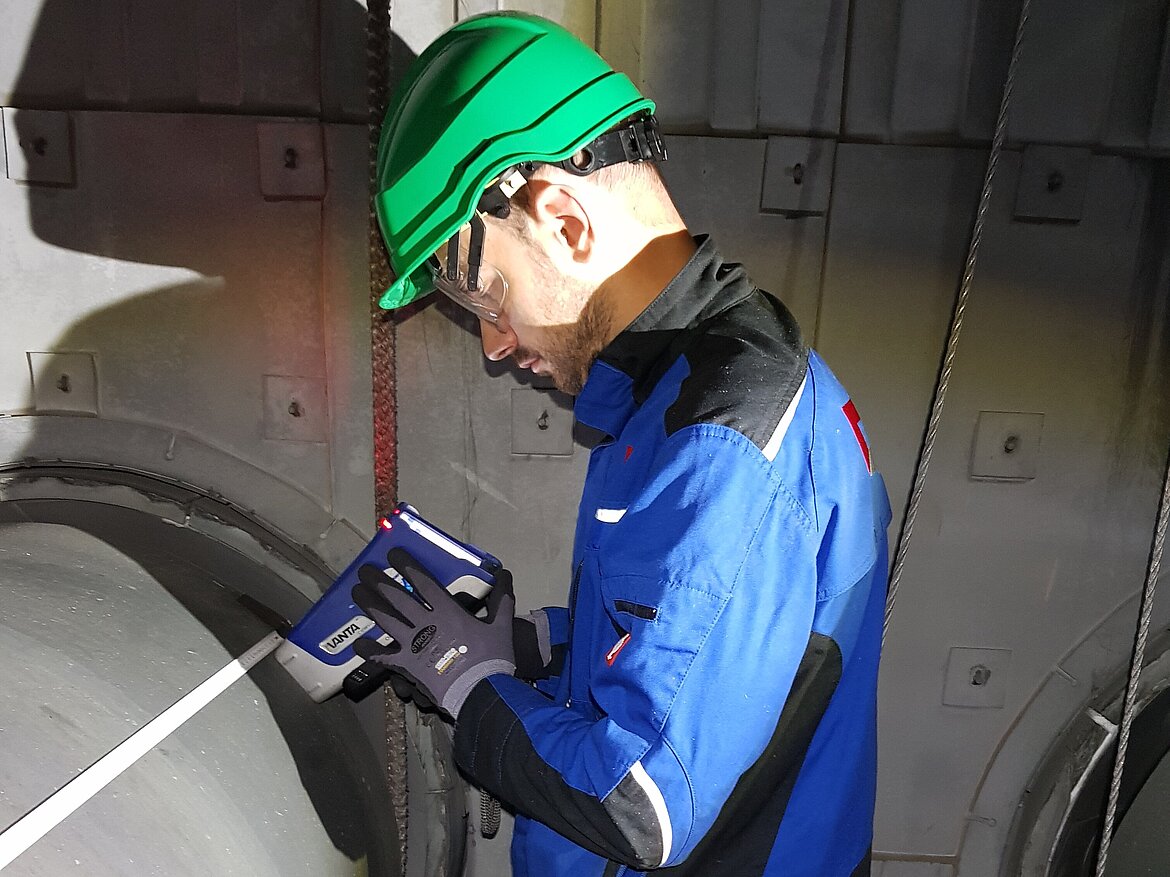
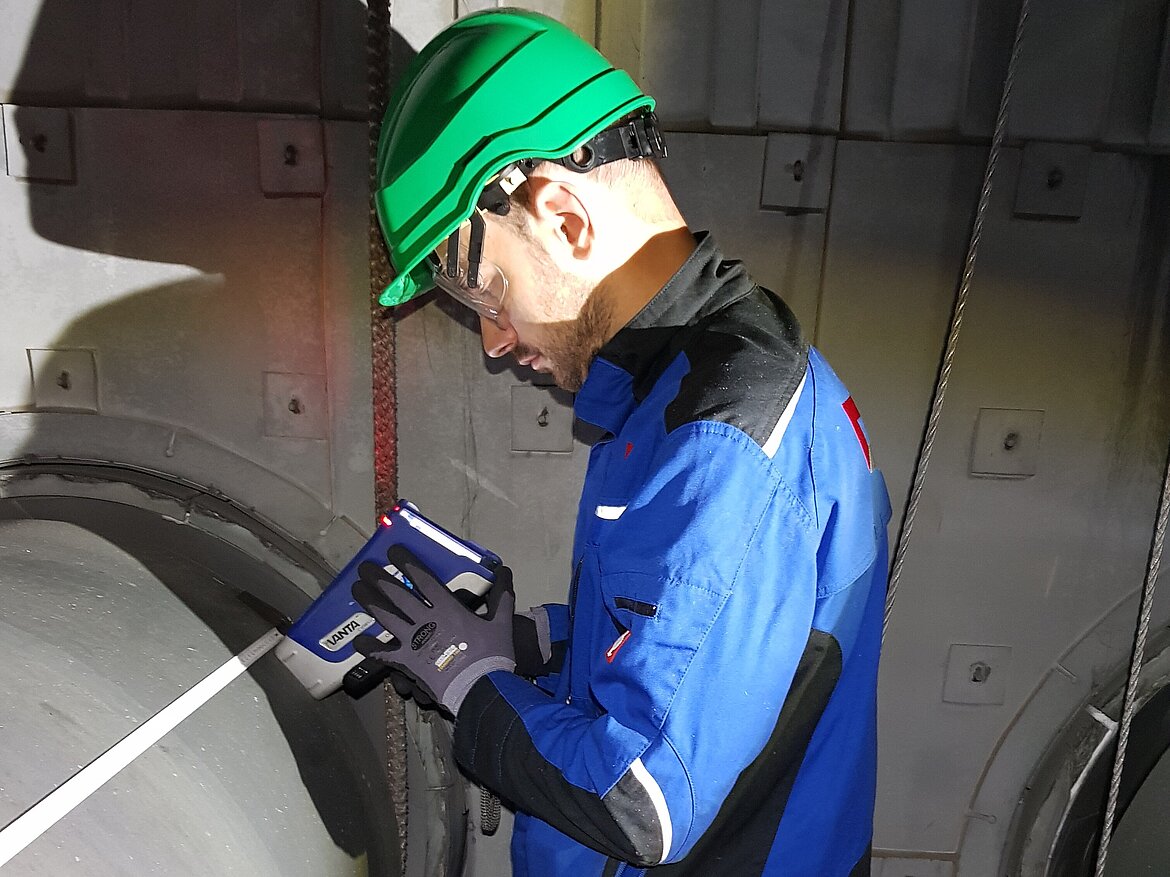
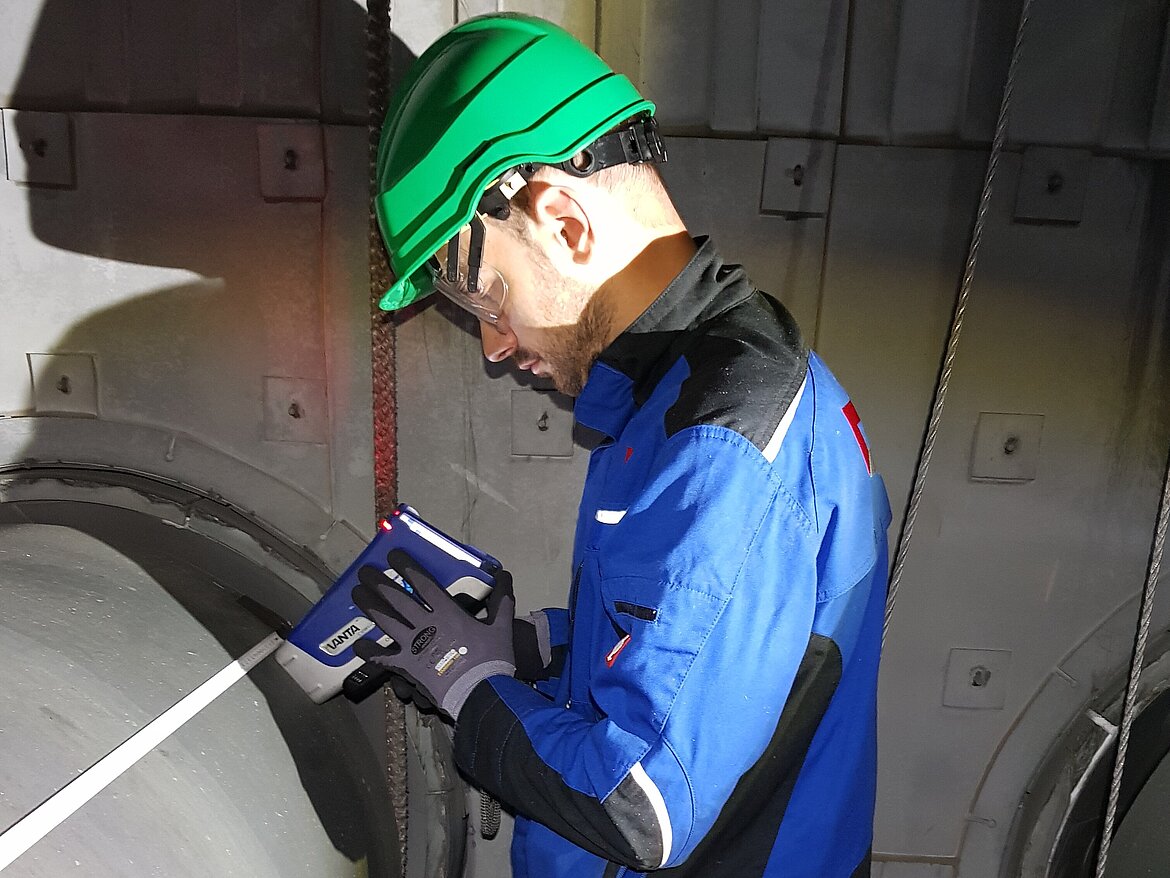
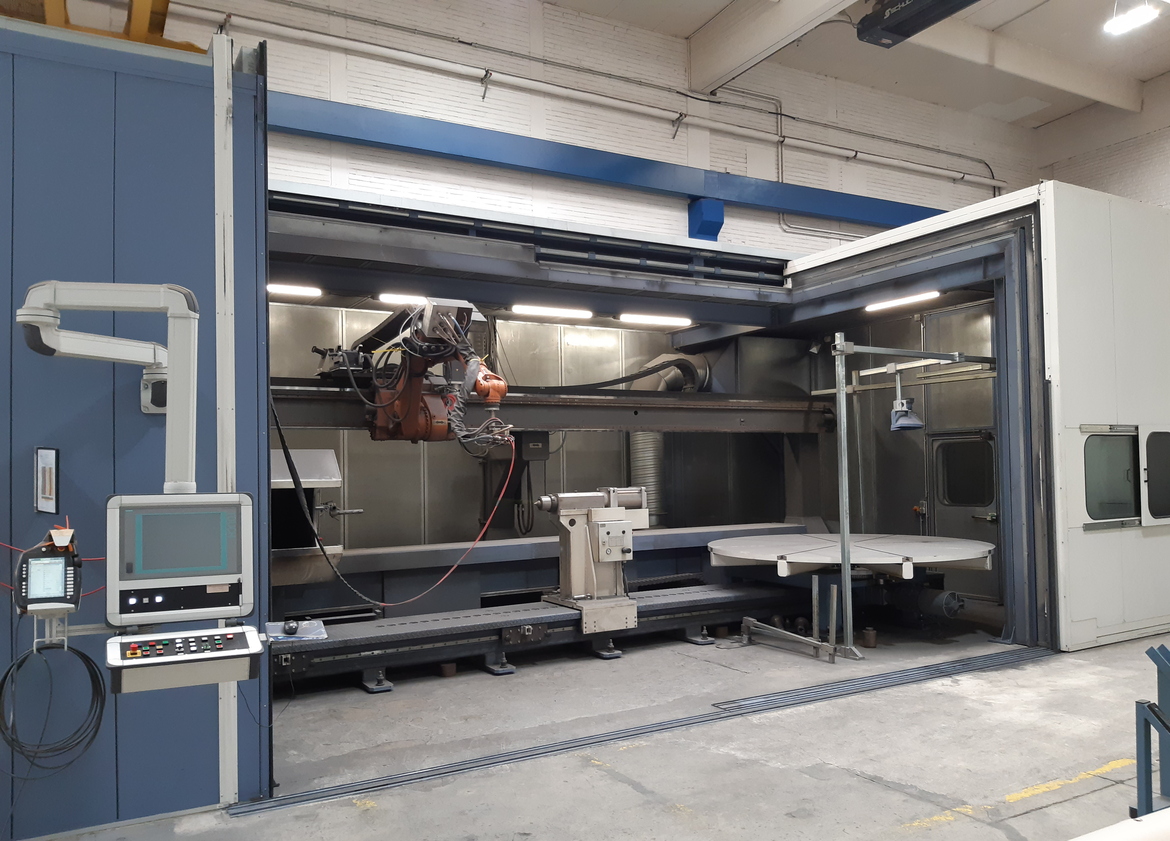
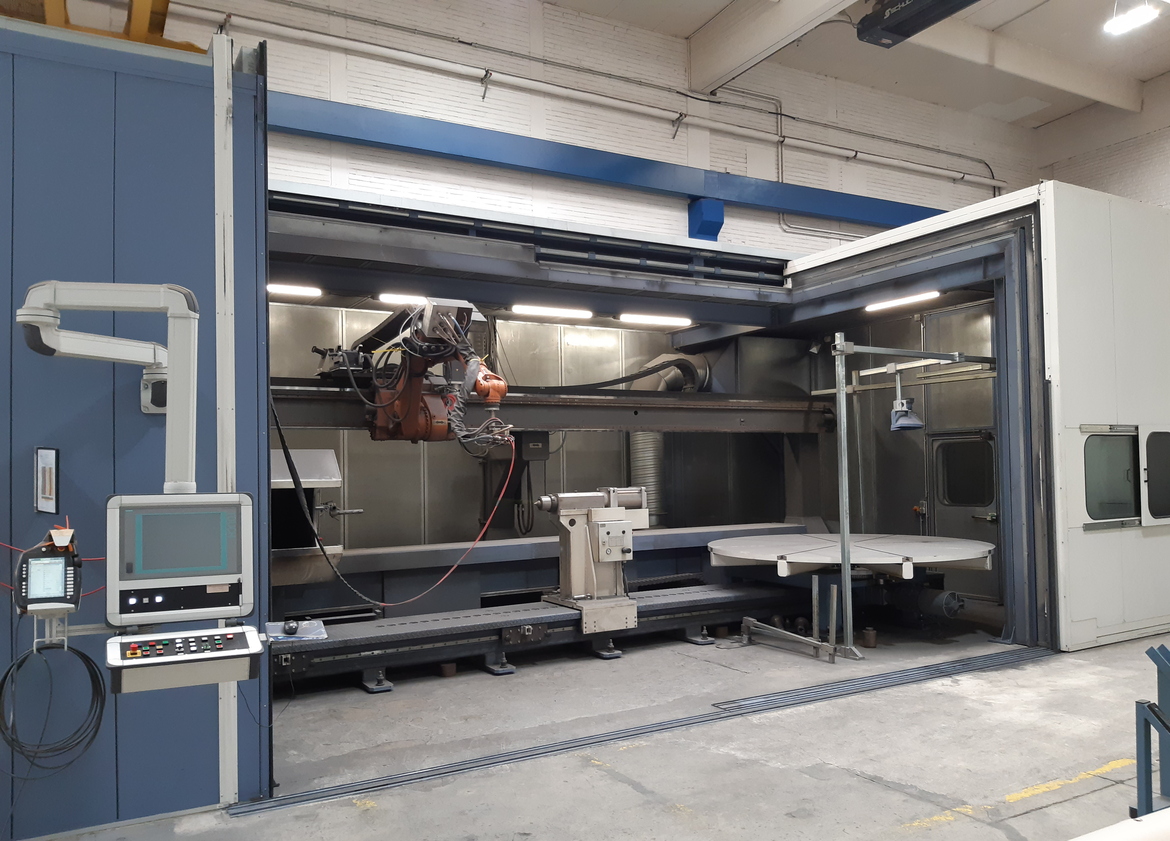
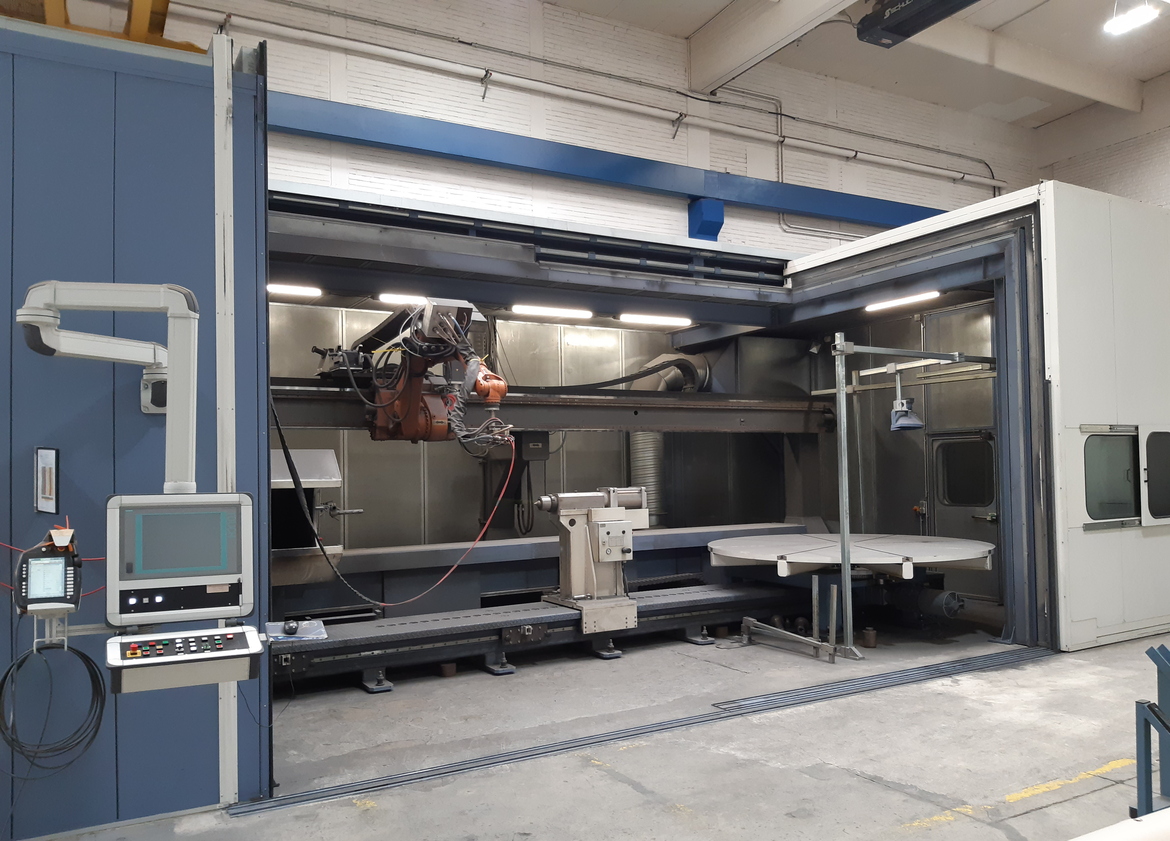
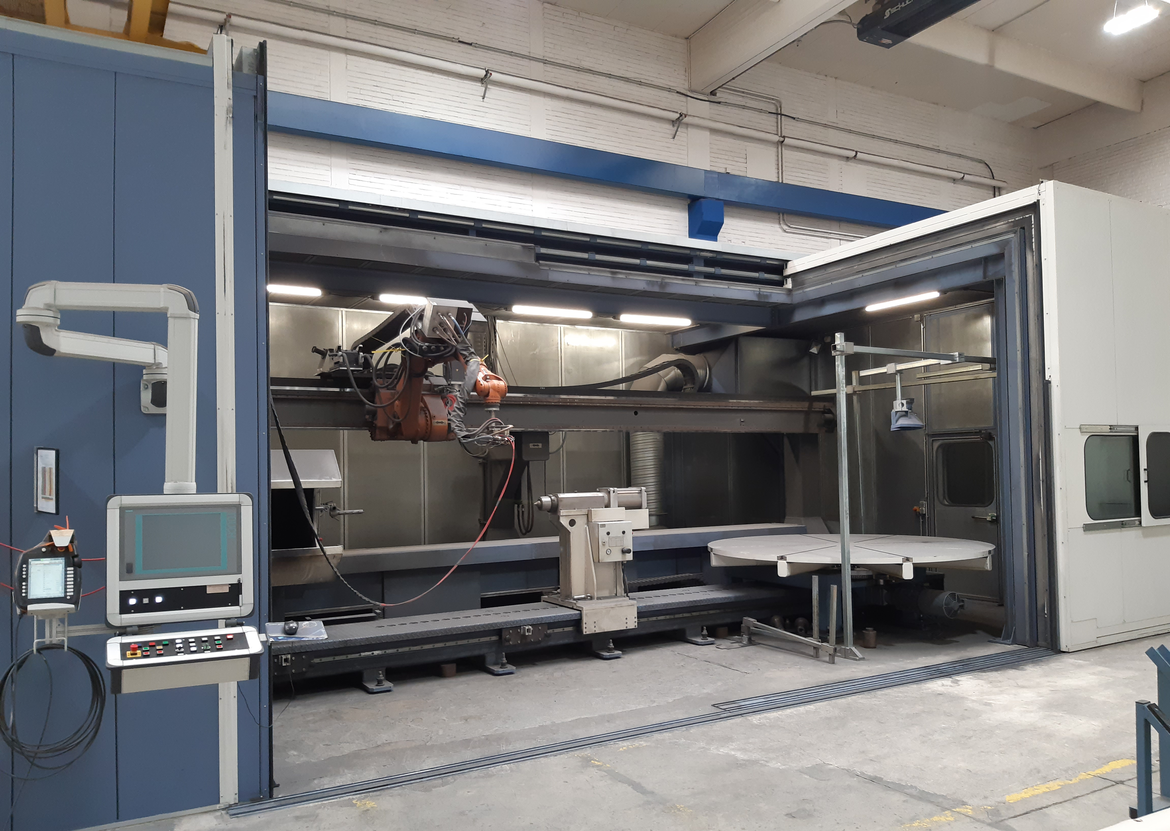
Coating Competence Center
Special coating techniques are used to make components particularly resilient. This trend continues to grow due to the cost pressure in general. What's more, the spotlight is shifting to coating processes for reconditioning worn components.
In order to better meet this trend worldwide, a centralized interdisciplinary project team has been built by SMS group experts from the fields of Long Products, Research/Development, Service together with their colleagues from the USA and us.
The newly created Coating Competence Center in Moenchengladbach plays a special role here. Our existing coating plant is used to handle components for our customers in the European market.
Next to already proven techniques new applications are also being tested on the plant and analyzed in the lab. This means that, from the middle of the year, all typical processes (HVOF, plasma and wire arc spraying) will be available.
- Currently, components with a size of up to ø1,600mm x 6,500 mm (max. 6,500 kg) can be coated
- Flat components up to 3,500 mm x 1,500 mm can be coated
- Since mid 2022 it is also possible to coat components up to ø 3,000 mm x 910 mm and 16,500 kg